Případové studie
APS pomohlo v Baumülleru uvolnit kapacity a zkrátit průběžnou dobu výroby na obrobně o 30%.
23.11.2021
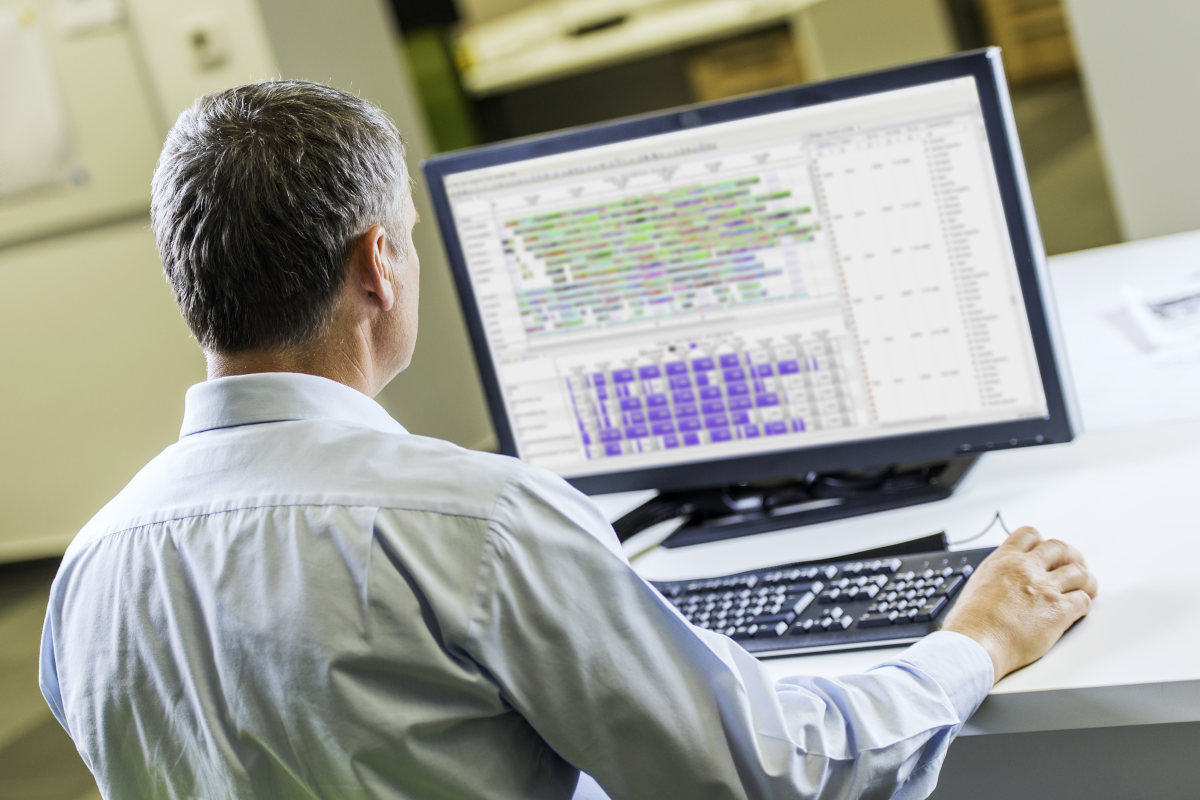
O společnosti
Společnost Baumüller Brno s.r.o. se zabývá výrobou elektrických pohonů a automatizačních systémů, které dodává do plastikářského průmyslu, výroby lodí, energetického průmyslu, ale i do potravinářství. Celosvětově má 40 poboček, z toho šest výrobních závodů v Německu, České republice, Slovinsku a Číně.
Proces výroby v Baumülleru Česká republika
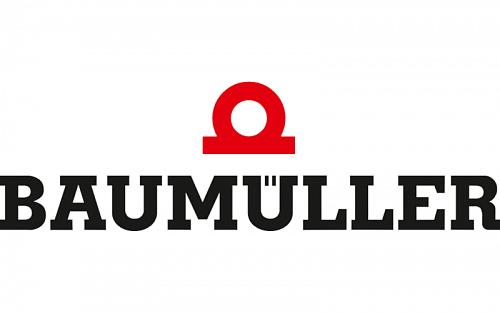
Baumüller vyrábí elektromotory, od obrábění odlitků až po finální motor. Disponuje čtyřmi provozy, kterými jsou obrobna, dvě montáže a finální montáž. Na obrobně je centrum obrábění a zalívání do zinku, v lisovně se razí plechy. V montáži montují rotory a statory a následuje finální montáž, kde se vše kompletuje. Otevřených operací a zakázek v systému má firma tisíce. Reálně se zde vyrobí až 160 finálních motorů a 600 statorů týdně, což jsou tisíce zakázek v různých fázích.
Objem zakázek a náročnost plánování si vyžádala software
Před implementací APS plánoval Baumüller v Excelu, kdy na každou úroveň výroby zadával plánovač výrobní plán, kdy má být co dokončené v rámci termínu. Neřešil však už konkrétní rozvržení ve výrobě, tzn. jednotlivé kapacity pracovišť v materiálovém toku apod. Mistři plán pouštěli 5 dní dopředu, ale nebylo jasné, jestli za těch 5 dní se stanovený objem skutečně vyrobí a nevznikne problém na nějakém pracovišti. Bylo třeba posunout plánování z mistrů na software a vědět, jestli je termín dokončení reálný. Další oblast, kterou firma potřebovala řešit, byla práce s daty. Nebyly údaje o plnění plánu, kapacitách, rozvrhování dopředu a výhled v rámci střednědobého plánu.
Bylo třeba dat, se kterými by mohli pracovat.
V ERP je možné kapacitní plánování, které ukáže problém, ale neumí správně přeplánovat. Cílem bylo redukovat průběžnou dobu výroby a redukovat rozpracovanou výrobu.
Volba systému a projekt
Na základě průzkumu trhu vydalo vedení v Německu závodu ve Skalici doporučení na APS Opcenter Scheduling (dříve Preactor) od společnosti Siemens. Pobočka ve Skalici v roce 2018 oslovila Minervu, jako dodavatele s poptávkou na studii na vlastních datech. Po shlédnutí demoverze a dodané studie nastala velká spokojenost s funkcionalitou systému. Nastoupila fáze přípravy dat, která trvala asi rok včetně testování dat s APS a customizace pravidel. V roce 2020 začala implementace APS Opcenter Scheduling. Přípravnou fázi prodloužil fakt, že pobočka ve Skalici nedisponuje vlastním IT oddělením a bylo třeba všechny požadavky řešit s IT v Německu.Termín dokončení celého projektu je plánovaný na konec roku 2021.
Nejdříve proběhla implementace v obrobně a montáži KTZ, kde je ukončená a předaná. Dle dohody je však Minerva stále k dispozici s podporou v rámci které probíhá ladění všech možností, jenž praxe odhalí a nastavují se další algoritmy. Díky složitosti výroby a množství vstupů, které se často neopakují, vyžaduje nastavování podmínek delší dobu.
Po ukončení provozu s podporou bude následovat příprava další montáže a finální montáže.
Znatelné přínosy již v průběhu projektu
Zavedením APS se projevilo ve snížení průběžné doby výroby na obrobně. Změnou a přínosem je, že neplánuje odd. Výroby, ale Plánování. Dříve nebyl jasně daný plán, co a kdy v té které fázi je třeba udělat. Nebylo možné vyžadovat splnění termínu po fázích. Další oblastí viditelného přínosu jsou aktuální data. Plánovač vidí, jak jsou vytížená pracoviště. Práce probíhá na základě dat, existují potřebné výstupy. Plánovač má více času, kterou věnuje exportu dat z APS do ERP, nahrává termíny do zakázek. Nemusí už termínovat zakázky v ERP, ale hlídá průběh zakázek v APS. Ošetřuje data, prochází pojistné zásoby, kapacity a hlídání termínů. Neřeší operativu, ale systémové věci.
„APS nám pomohlo uvolnit kapacity a zkrátit dobu výroby na obrobně o cca 30%. Pořízení plánovacího software byla pro naši společnost nutnost. Přínosem je logické plánování, které se složitě vyhodnocuje finančně, ale má nesporný přínos v rámci fungování celé firmy,“ vypočítává Jan Motyčka, vedoucí plánování v Baumülleru a dodává: „Na systému nejvíce oceňujeme reporty a simulace. Můžeme nasimulovat počet provozů, kapacity. Vidíme okamžitě dopad na konkrétní plán. Velkou výhodou jsou všechna data na jednom místě. Pracovníci mají přístup ke stejnému zdroji dat. Máme čtyři úrovně motoru, které do sebe vstupují a APS jednoduše zareaguje na všech místech v jednom plánu.“
Když zasáhne do projektu pandemie
V důsledku pandemie bylo nutné změnit styl práce ve vedení projektu. Osobní kontakty nahradila telefonická/online komunikace, což se ukázalo jako efektivnější způsob. Oblasti se řeší operativněji a po kratších objemech, což lidem v Baumülleru vyhovuje a je přínosné pro projekt jako takový.
Následné rozšíření do dalších závodů
Po ukončení celého projektu ve Skalici je v plánu zavést APS Opcenter Scheduling do dalších závodů v Německu. Očekává se, že tamější závody převezmou nastavenou strukturu pro APS a v závislosti na míry podobnosti výroby ji více či méně uplatní ve svých provozech.